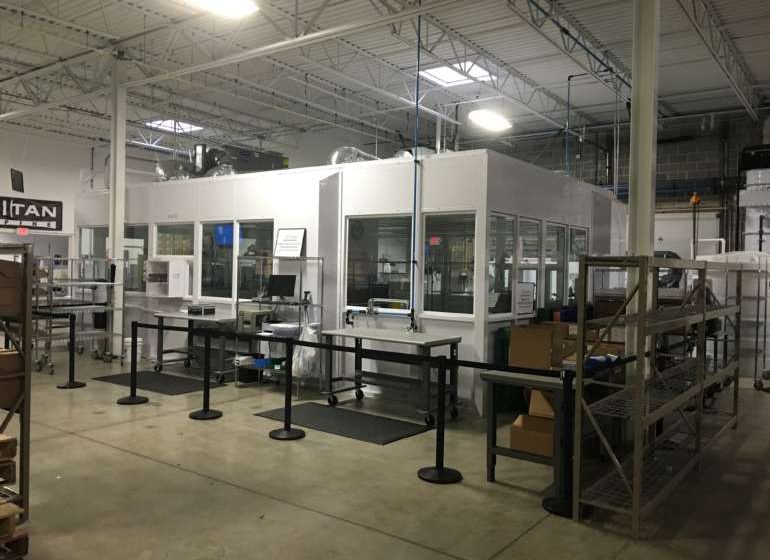
In a conference room across the hall from a wall covered in framed patent licenses at the Titan Spine headquarters in Mequon, company president Kevin Gemas digs through a box of spinal implants — some donut-shaped, some long and grooved — and describes them in a way that evokes a diagram of the evolution of man.
The bone-colored, plastic spinal implants are the past, he explains. The rough-surfaced, titanium implants made by Titan Spine are the future — for a few key reasons.
The company’s biggest roadblock in the 10 years since it was established has been overcoming a negative image of titanium devices that currently permeates the market, he says. He much prefers the company’s new problem: scaling.
“That’s our challenge right now,” Gemas said. “We can’t make enough.”
In February, Titan Spine announced it had increased sales 51 percent in 2015. Last year, its global sales totaled $33.5 million. Titan, which has 61 employees, more than 400 hospital customers and 110 distributors worldwide, also has a presence in Germany and Spain.
Gemas is a tall, broad-shouldered man. He played linebacker for the Clemson Tigers in the early 1980s and, though he didn’t start, was a member of the 1981 national championship team as a sophomore, donning No. 95.
He understands the importance of quick recovery from injury. And he, along with his close friend Dr. Peter Ullrich, Titan Spine’s chief executive officer and the brain behind its innovative line of titanium implant products, hopes their company will change the way surgeons and patients around the world approach spinal implants.
So far, their efforts are working, and their fast growth in the past two years has Ullrich and Gemas brimming with confidence.
“We have set out that we’re going to grow 59 percent this year, but I’ll be very disappointed if that’s all we do,” Ullrich said.
The backbone of the medical device manufacturer’s business is scientific research and data, Ullrich said, which he thinks has already given his company an edge in the market. But it will play an even larger role in the company’s future once its newest and most innovate line of products, which incorporate nanotechnology, hit the market over the summer.
“We really are a company now that’s on the forefront of regenerative medicine through nanotechnology, Ullrich said.”
The science
Ullrich was an orthopedic surgeon for 19 years and he felt the plastic, bone-colored spinal devices inserted between vertebrae during spinal fusion surgeries could be improved. What he wanted was a device he could insert between vertebrae that supported the hard, outer edges of bone but had a large, easily accessible opening in the middle for bone grafts.
He eventually developed a titanium prototype that would serve as the basis of the company’s product line.
Some early titanium implant designs that preceded Ullrich’s had a reputation for collapsing and forcing patients to undergo, in some cases, multiple follow-up surgeries.
Ullrich contends the problem stemmed from their design rather than from the material itself, but a negative image of titanium products among surgeons and hospitals persisted, which initially made it difficult to carve out a place in the market.
As Ullrich continued his research to improve his devices, he noticed their use resulted in shorter recovery times for patients. With further research, he and his staff began to notice the texture of an implant’s surface could influence the way the body’s stem cells regenerated tissue — a grooved surface caused the body to begin producing bone material much more quickly, whereas a smooth surface promoted the growth of fibrous tissue.
“The cells that attach to a device are what we call attachment-dependent cells,” Ullrich said. “And we didn’t know it when we started, but if they attach to this…”
He pointed to a smooth, plastic implant sitting on a table before him in Gemas’ office.
“…it makes the cells want to produce fibrous tissue. If they attach to that…”
He pointed to a textured, titanium implant.
“…it makes them want to produce bone tissue.”
The discovery led Ullrich to develop a device with tiny grooves the size of a nanometer on its surface. The grooves are so small, they’re impossible to detect with the human eye.
“We’re talking about atomic-level structures,” Ullrich said. “There’s 100,000 nanometers in the thickness of a piece of paper, so it is nothing that we can sense. But on the cellular level, that’s meaningful to the cells. What it does is it causes the cells to up-regulate the production of messenger RNAs that code for the other cells all becoming bone cells, too. So this is actually helping create the bone on the interior cage.
“Cells want to be in a pit, an osteoclastic-like pit,” he continued. “The big thing is whether or not the surface feels safe or not safe. They can become fiber tissue or bone tissue depending on what they sense.”
Among the benefits of the nano-grooves are reduced inflammation, fast bone growth and a dramatically reduced overall recovery time.
“The reparative phase starts within days and weeks,” Ullrich said. “We’re providing an implant that heals much more quickly.”
He used to tell patients to avoid physical activity for at least three to six months after spinal fusion surgery “now, we let them do whatever they want,” he said. “And it’s a big surgery.”
Titan Spine recently received clearance from the U.S. Food and Drug Administration to begin marketing and selling its nanotech device, and plans to ramp-up production at a facility in Brown Deer this year.