Perhaps no single issue has been more at the forefront of manufacturing discussions over the last several years than the skills gap. The idea that employers are not able to find enough potential employees to fill their needs has been a topic at seminars and conferences and has drawn the attention of both the press and lawmakers.
While some researchers have questioned whether the skills gap is really just a wage gap, the issue ultimately boils down to a question facing almost every industry: Where will the next generation of workers come from?
Like many industries, manufacturing faces a looming wave of retirements by baby boomers. According to U.S. Census Bureau data, 25.6 percent of Wisconsin’s manufacturing workforce is older than 55, up from 21.5 percent at the end of 2010.
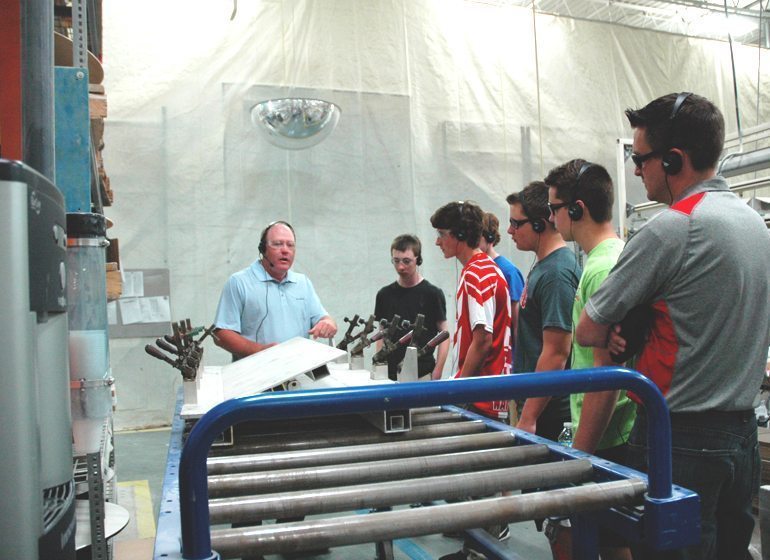
“If nothing is done within the next five to seven years, they’re all going to be hurting severely,” said Mark Hoedel, a welding instructor at Lynde and Harry Bradley Technology and Trade School.
That same data also shows a few bright spots for manufacturers, as it appears more young people are taking an interest in the industry. Those younger than 24 make up almost 7 percent of the manufacturing workforce and the number of workers in that age group is up 24 percent, to 30,331.
Manufacturing now accounts for 10.6 percent of those younger than 24 in the overall workforce, up from 8.5 percent at the end of 2010.
“When they start hearing what kind of money can be made straight out of high school, their eyes kind of light up,” Hoedel said of his students.
There’s also been progress at the state’s technical colleges, with enrollment in manufacturing programs up 35.6 percent from 2011 to 2015. Waukesha County Technical College and Milwaukee Area Technical College were among the biggest gainers, increasing program enrollment 54.3 and 53.5 percent, respectively.
“There’s been progress in the awareness element,” said Stephanie Borowski, president of Butler-based GPS Education Partners. “I think where we’re still lacking is young people seeing advanced manufacturing and technical education as a long-term career option.”
For GPS student Dewain Roberts, the potential for a career path became clear during his time in the program. He wanted to be an architect when he first heard about GPS as a 16-year-old at James Madison High School. He has had placements at Glenn Rieder, Perlick and Strattec, and now plans to go into mechanical engineering. He also has a 10-year plan that starts with going to MATC and ends with a master’s degree.
Roberts is hoping to land a job someday that is hands-on, something where he spends some time at a desk and some time testing out ideas. He said one of his biggest concerns was having a boring job.
“I thought manufacturing was mostly working on the floor all day, not actually really learning anything, just getting by,” he said.
For some it is, Roberts said, but for those willing to learn and work, there are opportunities to advance.
GPS Education Partners is at one end of a spectrum of programming that was developed to address the skills gap.
That spectrum also includes youth apprenticeships, internships, dual enrollment programs, high school lab areas and tours of facilities for students.
“I think it’s starting to finally get momentum because you’ve got the executives talking about it,” said Bryan Mullett, chief strategy officer at Menomonee Falls-based Bradley Corp.
Bradley is among the companies providing funding and industry guidance to the Arrowhead High School Design Engineering Manufacturing Center, a 10,000-square-foot facility that added a number of labs to the school’s campus.
Students toured Bradley’s facility last month and heard about how the company develops new products.
Organizations like the Waukesha County Business Alliance, Metropolitan Milwaukee Association of Commerce and MATC have taken thousands of students on tours of manufacturing facilities.
“The manufacturers themselves have done a great job of opening up their facilities,” said Dorothy Walker, MATC dean of applied science and technology.
With so many different programs, it would seem there’s potential for resources to be stretched thin and problems to arise.
“I feel like everybody’s pushing in the same direction,” said Amanda Payne, vice president of public policy at WCBA, adding that each program takes a slightly different approach and she has seen a lot of collaboration.
Susan Koehn, Milwaukee 7 director of industry partnerships, said she encourages businesses to look at developing their workforce as part of the supply chain and if there were fewer programs, companies may be discouraged if one didn’t work for them.
“There’s never going to be a one size fits all solution,” she said.
David Mitchell, president of Milwaukee-based Monarch Corp. and a participant in several state and local workforce initiatives, said he also has seen a lot of collaboration and all the programs help identify best practices. Wisconsin is ahead of the curve in addressing workforce issues, he said.
“I don’t think we take time to step back and look at the rest of the nation,” Mitchell said.
Despite the progress, manufacturing still faces the prospect of parents and students shying away from manufacturing careers when large layoffs happen at local companies.
“I think that’s a huge battle,” Payne said.
She said people pay attention to media reports and may not know about a smaller company with 15 openings.
“Unfortunately, you get one big headline about layoffs and that can be very damaging for the perception,” she said.
To that end, a number of manufacturers have started exploring ways to share their workforce with each other. Mitchell said the idea is when one is having a slow period, employees can work elsewhere and return when things pick up.
“We know our guys. I know every guy on the floor by name,” Mitchell said. “When we have to lay people off, we hate it.”
The idea has potential to work well among manufacturers who know and trust each other.
“The trick is, how do you scale something like that with companies that don’t have that longevity of relationships?” Koehn asked