Henry Medeiros
Marquette University
College of Engineering
Innovation: Improved robot mobility
www.marquette.edu
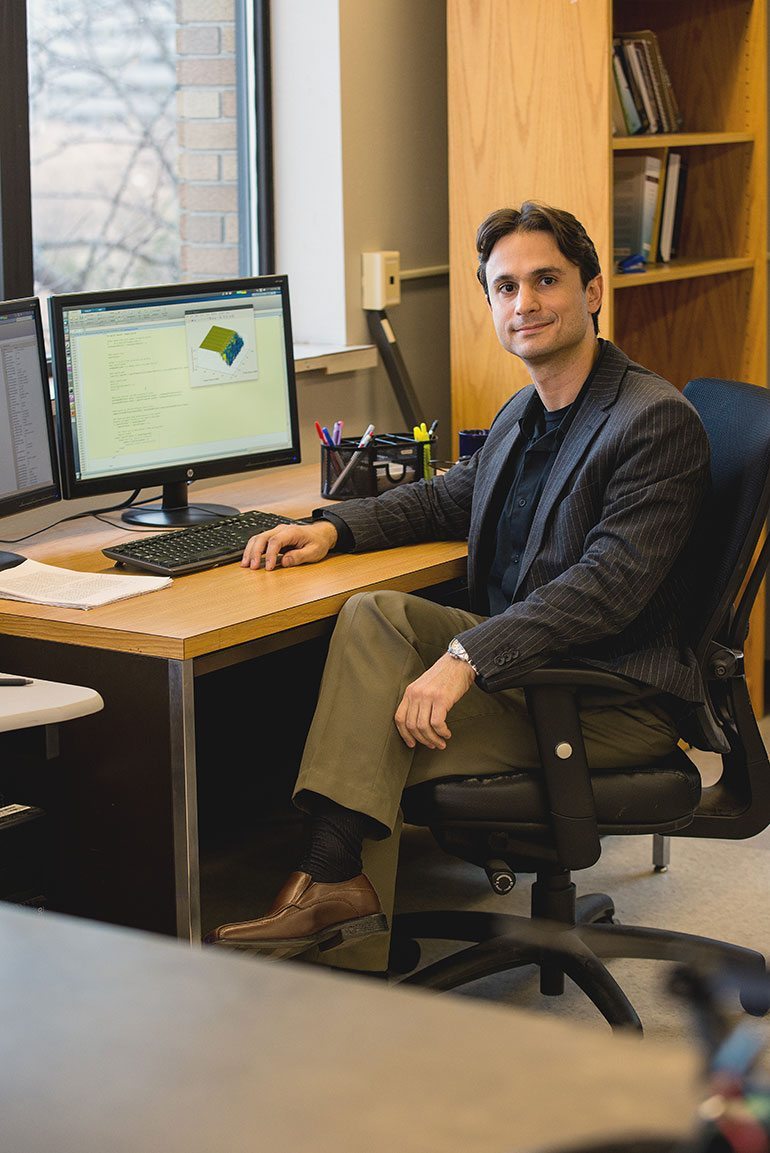
Plenty has been made of the potential for automation and robotics to change how products are manufactured. They offer the chance to improve productivity or remove employees from repetitive or dangerous tasks.
Use and adoption of robotics in manufacturing continues to grow. More than 240,000 industrial robots were sold in 2015 – a record, according to the International Federation of Robotics. That figure included 34,000 units in North America, an 11 percent increase over the previous year.
Robots have long been used in the automotive industry, but the number of applications in other industries has been increasing. Automotive OEMs and component manufacturers accounted for 69 percent of North American robot orders in 2005. By 2013, that number was down to 56 percent, according to a 2014 report by PricewaterhouseCoopers and The Manufacturing Institute. Food and consumer goods, semiconductors, life science and plastics contributed to the decline.
While costs have been coming down and the number of applications have been increasing, Henry Medeiros, a Marquette University assistant professor of electrical and computer engineering, said most robots are still set up in large, stationary cells. These robots can be programmed to perform the same tasks over and over. While large companies can afford the necessary investment, Medeiros said smaller manufacturers can’t afford robotics or would need to use them in multiple situations to justify the cost.
A 2014 PWC survey found 26 percent of manufacturers felt their use of robotics would be limited by the technology not being cost effective, and another 27 percent said they didn’t see a need for robotics.
Medeiros and a team of researchers at Marquette hope to expand the number of applications for robotics. They’ve received a $260,000 grant from the National Institute of Standards and Technology to improve the accuracy of mobile robots in manufacturing.
Robotic arms that move along six degrees of freedom are used frequently in manufacturing and automated vehicles that can move materials also are seeing increased adoption. Combining those two items – a robotic arm on a moving platform – presents a number of challenges when it comes to the accuracy required for manufacturing.
If the platform stops to perform each task as it moves from point to point, the robotic arm can maintain its accuracy. But stopping at each task when a manufacturer is looking to have a robot perform a number of tasks, and have it easily retasked, is problematic.
“What we want to do is take another step forward and do that with the robot in motion,” Medeiros said.
One approach is to move the platform to a known point, but even small errors can accumulate from task to task, throwing off the accuracy of the robot. Another approach could call for a patterned search to locate the starting point for each task, but it would require the platform to stop to maintain accuracy.
“It sort of breaks down,” Medeiros said.
His approach calls for repeatedly calculating the probable location of the next task as the platform moves closer and closer.
After developing mathematical models for this approach with simulations, Medeiros plans to begin real-world tests with a robot and platform in early January. The tests will allow him to quantify the errors with this approach and refine the models.
The plan for the two-year project calls for full-scale tests with robots identical to those used by NIST. If his ideas prove correct, Medeiros said the technology could be used in certain robotics right away.
Turning his development into an actual commercial application is a bigger problem and could take longer. Medeiros noted different companies may have different needs – one might need a robot to manipulate items while moving, another might just have it pick parts from an assembly line – potentially complicating the challenge.