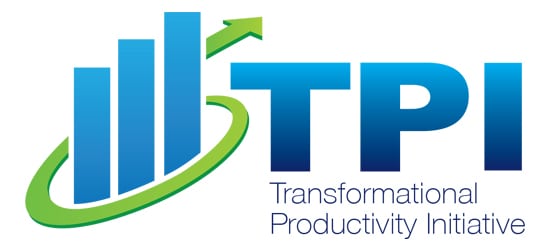
Manufacturers who recognize the need to take a comprehensive approach in addressing worker shortages are turning to the Wisconsin Manufacturing Extension Partnership’s Transformational Productivity Initiative (TPI).
What is TPI?
The TPI model presumes that productivity gains of 40 percent or more are both possible and necessary for manufacturers committed and willing to invest the time and resources required to transform all aspects of production. Transformational productivity methods and results are based on extensive research. TPI is a journey that will take place over multiple years and achieve expected improvements of 30 to 40 percent in overall productivity, including gains in labor efficiency.
It is well documented that top-performing companies in an industry sector are twice as productive as their lower-performing competitors. There are many reasons for this. The TPI process is designed to help individual organizations benchmark where they stand relative to top performers while identifying, prioritizing and, over time, closing performance gaps.
More efficient labor
Productivity is crucial for companies as a measure of efficiency. Chronic labor shortages are plaguing manufacturers, who often can’t ship enough product to meet customer demand. Taking steps to have more efficient labor can address the issue, including implementing productivity initiatives aimed at increasing production and revenue with a company’s existing workforce.
Nearly every day, we speak with clients who lament about not having enough workers or employing a workforce not productive enough to meet demand, for a variety of different root causes. The growth of these companies is being constrained by their existing labor situations.
The TPI process recognizes that there are no silver bullets, and improvements are required in all aspects of the business, including planning and execution; human capital management and engagement; operational and enterprise excellence; finding and exploiting a company’s niche; and the use of automation, robotics and digital technologies.
In short, TPI is primarily about taking an integrated approach to doing more with less.
The goal is to improve productivity – measured as value added or revenue per employee – by 40 percent or more. For a manufacturer with 60 employees and $10 million in sales, this could result in maintaining current sales with 40 percent fewer people or increasing sales without a proportional increase in headcount.
In practice, TPI assesses a company’s current situation, helps it enhance and accelerate current strategies and prioritize and integrate assessment findings into future planning cycles.
Long-term partnership
We engage for the long haul and work with manufacturers to put in place or improve systems, processes and procedures to help them plan and manage improvements at a required and manageable pace that works for them. Our level of involvement will vary to support a client’s needs.
As part of the process, we connect manufacturers to an array of resources and service providers that will help them create a comprehensive and integrated solution. Transformational productivity is a journey with incremental gains realized along the way.
Here’s where we stand:
- The WMEP, working in conjunction with the University of Wisconsin and a manufacturing advisory team, has developed a set of productivity assessments tools that cover all aspects of the business.
- Tools have been piloted at four beta sites with productivity improvement projects already underway.
- Tools will continue to be developed and refined, particularly as they relate to automation, robotics and technology.
- The WMEP is currently seeking as many as 20 manufacturers willing to work with us, who recognize they need to act and are willing to invest the time and resources.
- In return, we can offer significant incentives, up to $15,000 per firm, to help offset the cost of our services.
- Ideal target company size is 50 to 150 employees with $10 million to $30 million in annual sales.
How it’s done
For most organizations, early gains will be realized by setting and communicating improvement targets, aligning organizational, departmental and individual performance goals, and engaging the entire workforce in structured daily and targeted rapid improvement projects covering both production and administrative activities.
As this foundation is built, improvement activity should expand to include automation of processes and information flow; introduction of robotics; and ultimately leveraging digital technologies to continue to drive improvements.
The entire business model, including every single aspect of what is produced and how it is produced, needs to be methodically scrutinized to set a course for improved productivity.
For more information about the Transformational Productivity Initiative and other offerings from the Wisconsin Manufacturing Extension Partnership, go to www.wmep.org.