Dorner Mfg. Corp.
975 Cottonwood Ave., Hartland
Industry: Conveyors
Employees: 250
www.dornerconveyors.com
Solving problems for customers through new product development is one way to keep and gain market share. But when those efforts start encroaching on manufacturing and production space, it can present a problem.
Hartland-based Dorner Mfg. answered the challenge with a 25,000-square-foot addition to its facility that opened earlier this year, bringing the total size to 170,000 square feet. The result was enough room for product development, along with a new laser cutter and break press.

Dorner designs and manufactures conveyor systems for a wide range of applications. Expanding into new markets, more aggressive marketing and new product advancements have helped the company grow substantially over the past few years. The growth has included adding 100 employees over the past three years.
Terry Schadeberg, Dorner chief executive officer, said the business model, which focuses on leading technology, high-quality products and short lead times, hasn’t changed much since the company was founded in 1966
“The Dorner brothers created it 50 years ago; I can’t take any credit for it,” Schadeberg said. “It resonated with the marketplace back then and it resonates with the marketplace today.”
Brothers Wolfgang and Horst Dorner founded the company as a tool and die shop. In the early 1970s, they were looking for a conveyor to remove scraps from underneath their dies and were told it wasn’t possible to fit one in the small space available. Their response was to develop a low profile model that was introduced in 1973. Before long, the tool and die business was phased out and the Dorners were in the business of making conveyors.
Today, Dorner’s products do more than just fit into tight spaces. Flexible belts allow conveyors to turn corners, sensors and cameras can make sure products are properly spaced, backlighting allows for better visual inspection and vacuums hold parts in place on the belt.
Dorner serves a number of industries, including food handling and processing, packaging, pharmaceutical, medical and general manufacturing. As manufacturers have increased their focus on automation and productivity, the needs for Dorner’s products also have developed.
“We’re dealing with pieces and units in a process,” Schadeberg said, explaining that having the exact speed, orientation and location becomes important when feeding into high-speed packaging, visual inspection systems or robotics. “We’re always kind of teamed up with much more expensive equipment that goes around (the conveyor).”
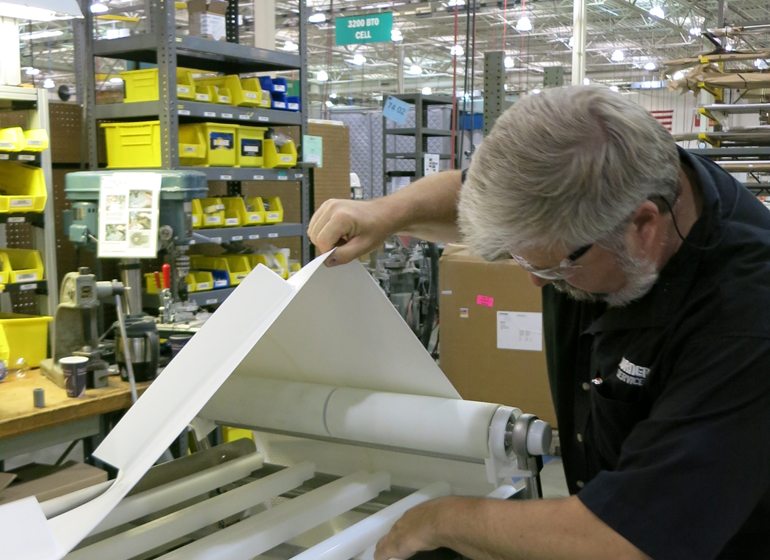
Schadeberg said competition in conveyor manufacturing is largely regionalized in the United States and Dorner is one of the few national players.
There’s also competition from overseas, particularly in Europe and Asia.
To better compete in international markets, Dorner has completed two acquisitions over the past year. The first was Malaysia-based FlexMove, a leading manufacturer of flexible chain conveyors. Schadeberg said the move would provide a “beachhead” company for Dorner to go after sales in the Pacific Rim and Asian markets.
In the same way, the acquisition of Geppert-Band, a German manufacturer of belt and modular belt conveyors, in May was intended to provide a base for European operations.
Schadeberg said one of the biggest challenges remains finding the right employees, particularly in engineering.
In production, the company has gotten creative, with a group of 12 to 16 on-call employees. This group of mainly college students and retirees provides their available hours and the company lets each know if there is work available. The on-call employees work up to 24 hours each week. The positions don’t come with many benefits, although there is an hourly premium. As a result, Dorner can flex staffing up or down to meet demand.
In engineering, though, Schadeberg said the challenge is continuing to stay ahead of a rapidly advancing technology curve.
Get the latest manufacturing news delivered to your inbox every Monday. Sign up for BizTimes’ Manufacturing Weekly at biztimes.com/subscribe.