Taylor Dynamometer
3602 W. Wheelhouse Road, Milwaukee
Industry: Measuring and control device manufacturing
Employees: 50
www.taylordyno.com
There’s a good chance those who bring their trucks to tailgate at Miller Park can thank the folks at Taylor Dynamometer, located not far from the eastern parking lots, for their vehicles’ reliability.
Taylor Dynamometer has been around for nearly 90 years, but it has been within the last 16 years that the company has grown and expanded. President Art Downey became an owner in 1999 and vice president of sales and marketing Jeff Brown joined him in 2000. Vice president of engineering Larry Golding joined them a few years later.
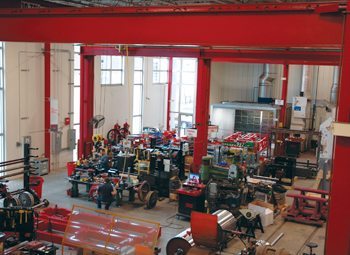
The new ownership has expanded Taylor’s offerings, but engine dynamometers are still at the core, just as they have been since the 1940s. The dynos test engines for force, torque and power. They are used to verify repairs, validate specifications, break in new engines, check an engine rebuild, or in research and design testing. Taylor builds models that can test engines from 50 to 10,000 horsepower.
Taylor also makes chassis dynamometers for testing semi-tractors and towing dynamometers that aide in truck development for most of the large auto original equipment manufacturers.
While dynamometers have long been the heart of Taylor’s business, the company has shifted into other products and services to fuel its recent growth. That includes designs and products for engine test cells.
Downey said Taylor realized customers were only building new test cells every 10 years. The process involves moving air, water and fuel through the room and customers would have to completely relearn how to properly set everything up.
“They’re going to hire someone to do it for them one way or the other; it might as well be us, who’s supplying many of the components going into it,” Downey said.
Taylor also spent the last three years designing a hydraulic test center to improve on a previous product. It includes mechanical engineered parts combined with newer technology, a marriage that flows through much of Taylor’s work.
“It’s sort of like southern California is dating the industrial rust belt, which is fun. It’s sort of fun to see this really cool engineered stuff having a high-tech application,” Downey said.
The company builds data acquisition and control systems, which act as the brains of the testing system, in-house.
Taylor also maintains a service staff that travels throughout the world. A floor to ceiling map in the service department office features pins from all of the stops the team has made. It was started a few years ago and only includes a portion of the installations the company has made.
Most of the company’s business comes from exports, which means Taylor is facing a number of challenges from the world economy and a strong U.S. dollar. The company also sells into oil and gas and mining markets, which adds to the current challenge.
The company’s 52,000-square-foot facility, built in the mid-2000s, was also designed with the employee in mind. Downey recalled the company’s previous location in New Berlin, where there were three cinderblock walls between his office and a window. The windows on the shop floor were high off the ground and provided very little light.
The new facility features large windows, including floor-to-ceiling windows on the shop floor. There’s also a large cafeteria for employees and plenty of artwork to commemorate the company’s and Milwaukee’s history.
Downey and Brown said low turnover and solid relationships with temp agencies have helped avoid too many staffing issues. While Downey acknowledged it can be a little harder to work when the parking lots at Miller Park fill up and the grills are going, Taylor’s location in the Menomonee Valley also gives it a central location to draw talent.
“In the world of industrial parks, it’s about as nice as it gets,” Downey said of the Menomonee Valley.
Get the latest manufacturing news delivered to your inbox every Monday. Sign up for BizTimes’ Manufacturing Weekly at biztimes.com/subscribe.