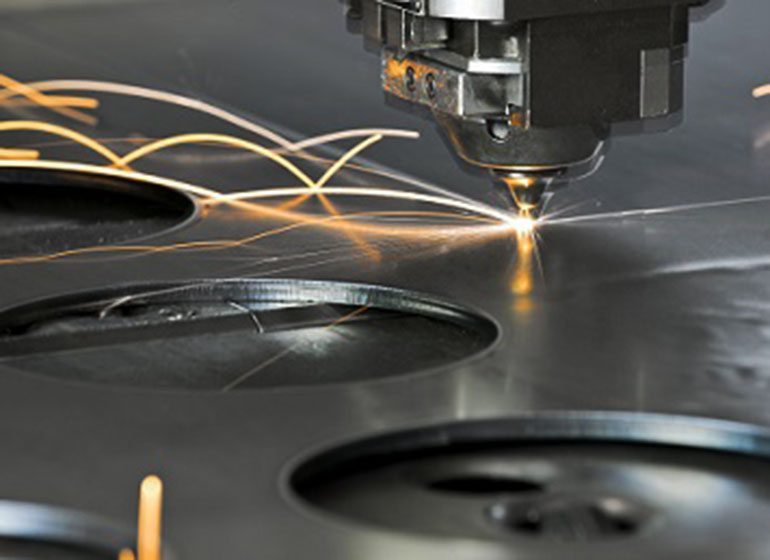
In an increasingly competitive global manufacturing market, WMEP has become a proven resource for Wisconsin-based companies looking to increase their worldwide footprint.
WMEP is a not-for-profit organization with deep expertise in helping small and midsize Wisconsin manufacturers achieve efficiencies and growth, as well as establish a collaborative culture and gain specific certifications. An affiliate of the National Institute of Standards and Technology’s Manufacturing Extension Partnership, which includes a network of 59 centers, WMEP directly assists Wisconsin companies on projects ranging from lean manufacturing and Six Sigma certifications to strategic planning, new product development and leadership advancement.
Program drives manufacturers’ profits, sustainability improvements
Through WMEP’s programs and services, Wisconsin-based companies have a competitive edge in a global market. One such program is PSI. Developed in response to the 2008 Next Generation Manufacturing Study, PSI launched in 2010 and has helped more than 225 Wisconsin manufacturers cut costs while enhancing the resource efficiency of their supply chain. Funded in part by WEDC, the program bridges the intersection of sustainability and profit by helping to improve resource utilization, increase profits and reduce risk and environmental impact. PSI brings together a team of energy, environmental, logistics and lean experts to work with manufacturers to identify and implement improvements.
Because of the PSI program, Wisconsin companies have experienced both immediate and recurring profitable sustainability outcomes with measurable ROI. These improvements, in turn, make them more competitive in the global market. As of November 2015, aggregate capital investments totaled $17 million and annual savings totaled $20 million—with an average ROI of 176 percent. On average, it takes participating companies only 10 months to recover the cost of investment in the PSI program.
“Sustainability is no longer an option,” said Randy Bertram, director of sustainability services at WMEP. “Major corporations including Walmart, McDonalds and 3M require suppliers to implement, track and report on their sustainable improvements. Because of PSI, Wisconsin manufacturers have an edge on their competitors in responding to these changing demands, and have access to resources not available in any other state.”
Quick Cable, based in Franksville, has reduced waste in the value stream by 14 percent, reduced the amount of raw material costs by 2 percent and increased throughput by 20 percent. The privately-owned company develops, manufactures and sells battery and electrical connectors, cable, tools and related products for commercial and industrial equipment.
As part of the program, a diagnostic of the company’s use of resources and manufacturing processes revealed that the best opportunity for savings and resource conservation was in process optimization. Using funds from the PSI program to install a new trim process, Quick Cable recovered and re-used the metal from its product. This reduced the amount of raw materials required and eliminated waste destined for the landfill, and lowered the amount of energy used because the grinders and drill press were no longer needed. In addition, the trim process expedited production by relieving a bottleneck, allowing employees to be deployed to other roles within the facility.
“Manufacturing processes that use resources efficiently and minimize environmental impact enhance the competitiveness and profitability of our business,” said Robert Hoganson, vice president of manufacturing for Quick Cable. “That’s why PSI was such a great fit for our company. Quick Cable’s market opportunities have expanded due to the growing demand for renewable energy sources – including batteries – so the PSI program timing was perfect.”
With the help of organizations like WMEP, Wisconsin companies like Quick Cable are advancing best practices related to process efficiency and sustainability. WEDC is honored to partner with WMEP and help fund these efforts to make companies in Wisconsin more competitive.
To learn more about the good things WMEP is making happen in Wisconsin, visit wmep.org.