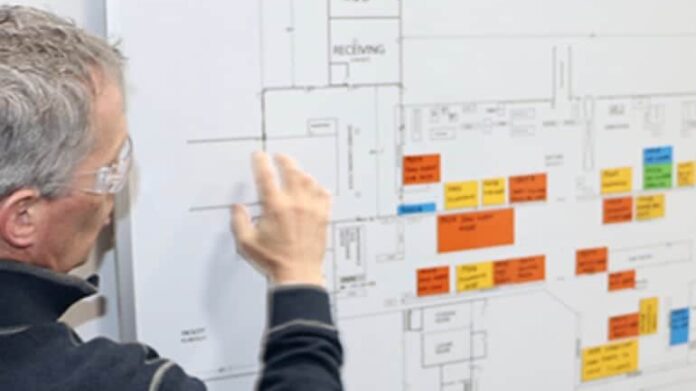
International Thermal Systems has committed to continuous improvement as a means of outpacing its competition, improving its bottom line and attracting and retaining key talent.
As part of this pledge, International Thermal Systems is in the second year of a burgeoning relationship with the Wisconsin Manufacturing Extension Partnership (WMEP), with a focus on a companywide lean transformation.
“Primarily, we’ve been focused on trying to educate people to understand what lean is and the concept of continuous improvement and trying to really drive a cultural change and a different mindset within the organization,” International Thermal Systems President Tom Stricker said.
The executive leadership at International Thermal Systems has recognized the need to continually look for ways to improve their processes, said Jerry Thiltgen, operational excellence manager for the WMEP.
“By improving processes, the company is better positioned to grow sales,” Thiltgen said.
The West Milwaukee-based industrial firm is essentially a conglomeration of four companies – LTG Technologies, which manufactures industrial ovens, washers and dryers used in manufacturing processes; Continental Equipment Corp., a unit that produces an industrial parts washer line; Industrial Heat Enterprises Inc., a provider of thermal and cleaning solutions; and Oven Systems Inc., a worldwide supplier in the battery and metal packaging industries.
Engineering, manufacturing and research and development functions are housed at the West Milwaukee site. The company’s newly expanded facility in Shanghai, China, provides additional engineering and manufacturing capacity and sales support. A sales office in Stuttgart, Germany, broadens the company’s presence in Europe, the Middle East and Africa.
International Thermal Systems’ workforce stands at about 105 employees, including 85 at the company’s 77,500-square-foot facility in West Milwaukee, with 15 to 20 at the facility in China.
International Thermal Systems turned to the WMEP at the recommendation of a colleague of Stricker.
“We liked the WMEP’s focus on Wisconsin manufacturing and the fact that the organization is Wisconsin based,” Stricker said. “And the pricing was reasonable, so we decided to work with the WMEP.”
Projects with the WMEP have included value-stream mapping exercises to improve throughput yield and a 5S workplace organization campaign involving various work cells on the shop floor.
International Thermal Systems has also conducted kaizen events – short duration improvement projects – to address specific issues.
“We’ve identified specific problems, and we’ve had a weeklong event where we’ve sat down and identified root causes and corrective steps and documented the process changes we made and then audited those processes,” Stricker said. “We’ve got a continuous improvement idea board, as well, where employees come up with their own ideas.”
International Thermal Systems has experienced an array of benefits from its lean transformation.
“One of the things that came out of a kaizen event was a reduction in warranty issues,” Stricker said. “We’ve seen a reduction in the cost of quality. We’ve also seen some efficiencies in time on the shop floor with the 5S events, reducing the multiple handling of some of the product.”
Changes have included receiving piping in the part of the shop where it’s needed and used.
“We used to receive it with everything else and it would be stored there and then shipped over to the piping area when it was needed,” Sticker said. “You had multiple touches on the product. Now, it’s very simple.”
Lean transformation has had a positive effect on International Thermal Systems’ bottom line, Stricker said.
“The prime example is reducing warranty costs, which is contributing directly to the bottom line,” Stricker said. “I do fundamentally believe that it will help us with the top line as well.”
The relationship between International Thermal Systems and the WMEP is continuing, with several other projects currently being mapped out.
The WMEP is continuing to support the cultural transition at International Thermal Systems by promoting employee engagement and recognizing how leadership behaviors support or hinder the process, Thiltgen said.
The WMEP’s wide-ranging experience in continuous improvement has been highly beneficial for International Thermal Systems, Stricker said.
“What the WMEP has is a perspective of having seen lean in so many other organizations and environments,” he said.
For more information about continuous improvement programs and other offerings from the Wisconsin Manufacturing Extension Partnership, go to www.wmep.org.