Brady Corp.
6555 W. Good Hope Road, Milwaukee
Industry: Identification and safety solutions
Employees: 6,400
www.bradycorp.com
From a safety sign on an oil rig in the North Sea to the bracelets put on newborn babies in the hospital, Milwaukee-based Brady Corp. has been developing and manufacturing a variety of identification and safety materials for 100 years.
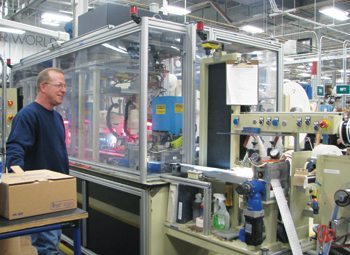
“There’s a common thread that runs through all of our products, and that’s high performance,” said chief financial officer Aaron Pearce. “For example, we sell a lot of labels, but you will never see a Brady label on a shampoo bottle or can of beans. Where you’ll see Brady products are in much harsher environments or where performance is absolutely critical.”
For instance, the federal government contracted with Brady during World War II to make wire markers for aircraft.
Meant to easily identify a plane’s hundreds of miles of wires, the wire markers were built to remain adhesive and legible in extreme conditions, such as when the temperature is -50 degrees when the plane is 30,000 feet in the air or is at 150 degrees while sitting on an Asian Pacific tarmac.
The wire makers also had to be capable of withstanding potential jet fuel spillage and contain properties that would not create noxious gas if the plane were to catch on fire.
Those wire markers were one of Brady’s earliest products and one that is still manufactured today, albeit with higher technology.
Labels, signs, tags and other workplace safety products make up one-third of Brady’s current sales, while the other two-thirds of its sales fall into the identification solutions business platform that includes such products as name badges and employee ID cards.
Here in Milwaukee, where Brady employs about 1,000 people, the products are made in one of its two manufacturing facilities. The plant at its global headquarters at 6555 W. Good Hope Road in Milwaukee is 105,000 square feet, and the other, at 2221 W. Camden
Road in Glendale, is approximately 200,000 square feet.
materials for a variety of industries.
About one-third of its products are produced and shipped from Milwaukee.
Brady also operates manufacturing facilities in Buffalo, N.Y.; Lexington, Ky.; and Tijuana, Mexico. Under the facility consolidation plan it started two years ago, Brady has reduced its North America manufacturing locations from eight to four to improve efficiencies.
Brady, which makes its products through the processes of printing and converting, also plans to consolidate its facilities in Europe and Asia by the end of 2017.
Another strong initiative of Brady’s is research and development, an area in which it has invested $180 million over the past five years. Last year, Pearce said the company spent about $35 million, and this year it plans to invest $40 million in R&D.
Innovation is important to stay ahead of competitors, according to Pearce, who said that current areas of interest in research and development include data-containing materials, like labels and wristbands, and enhanced printer platforms.
While Brady serves myriad industries, such as telecommunications, construction and education, it is also focusing on providing more new proprietary products for the food and beverage processing; chemical, oil and gas; medical; and aerospace, defense and mass transit industries.
With Milwaukee being the home of the global headquarters, the research and development center, the centralized distribution center and manufacturing, Pearce said not a day goes by that Brady is not hiring.
Currently, about 30 positions are open at Brady in Milwaukee, many of which are in the areas of engineering and research and development.
Brady, which moved its headquarters from Eau Claire to Milwaukee in the ‘40s, operates 80 sites in 31 countries. Its 2014 revenue was $1.23 billion.