Astronautics Corp. of America
4115 N. Teutonia Ave., Milwaukee (headquarters)
1426 W. National Ave., Milwaukee (manufacturing)
Industry: Avionics
www.astronautics.com
If you take your tablet to the beach and accidentally leave it in the sun, it may overheat and shut down. Not a problem; Take it somewhere cooler, wait a little bit and it will likely restart.
Put a similar tablet in an airplane cockpit and use it for any number of tasks related to flying and, suddenly, shutting down and waiting to restart is not an option.
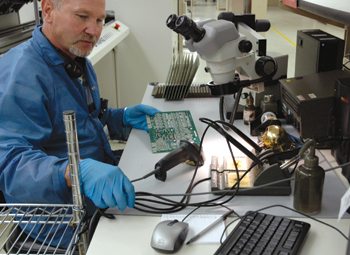
That’s the challenge Chad Cundiff and his team at Milwaukee-based Astronautics Corp. of America faces on a daily basis.
“Good enough doesn’t really apply in the vocabulary we have around here or that the industry really has been built on,” said Cundiff, president of Astronautics.
The company, founded in 1959 by Nathaniel Zalazo and Norma Paige, designs and builds avionics systems for aircraft in the civilian, defense and space industries. The idea is to take new technologies, often driven by advances in consumer products, and apply them to aircraft.
The devices are used for displaying information, providing guidance and navigation, automating flight and connecting with the ground, and they need to work without fail.
That’s why half the cost to design a new product is spent on verifying it will work, versus just designing it in the first place. It’s also why electrical components are tested at each step as they move through the manufacturing process.
“The earlier you detect (a problem), the better it is” said Karen Schlomann, Astronautics’ director of process and development control.
Each device undergoes several hours of testing during the assembly process, plus a 40-hour environmental test that vibrates it and takes it through a temperature range of -50 degrees to 50 degrees Celsius.
The manufacturing process includes placing components on printed circuit boards, assembling them into housings and connecting them to display units.
Each program Astronautics builds products for puts a different demand on the manufacturing operation. Some are built every couple months.
Others, like those used in the Boeing 787, are made on a monthly basis. An average of 150 units are produced each month. A separate repair unit handles 200 units per month, some dating back to the 1960s.
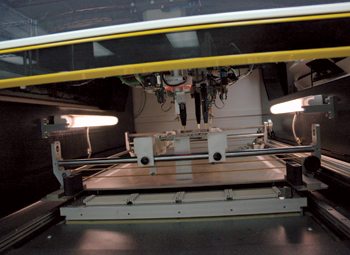
To handle the variation, the company is moving toward using flexible cells for production, instead of having space dedicated to each program. As technology makes devices smaller and more complex, taking the assembly process into consideration during design becomes more important.
“We’ve come a long way in the design for manufacturability,” Schlomann said.
Part of the challenge for Astronautics is to design products that are safe while also making them lighter, stronger and more cost-effective, Cundiff said, noting that costs ultimately are paid by consumers.
The design process has to emphasize not only coming up with new ideas, but also verifying that the product requirements are met, something Cundiff said is built into working at Astronautics.
He said much of the engineering curriculum in universities is focused on developing new ideas, and not as much on verification.
In an effort to increase the emphasis on the latter and attract people to the aerospace industry, Astronautics is leading an effort to start a center of excellence similar to other industry clusters in the area.
“There’s still a lot to be done for this industry,” he said, noting air travel has become remarkably safer over the past 20 years, but there are still opportunities to make flying more efficient.
After spending a decade working on a network server program for Airbus, Cundiff said he is looking to reinvigorate the company’s history of innovation.
One example is its RoadRunner Electronic Flight Instrument, a device that replaces older mechanical instruments on helicopters. It adds functionality, gives a view of the terrain and can alert the pilot to obstacles.
Cundiff, who came to Astronautics three years ago after working at the likes of Boeing and Honeywell, said he likes the company because it’s large enough to take on big projects and small enough to react quickly.
“There’s a real emphasis on doing new and innovative things,” he said.
-Get the latest manufacturing news delivered to your inbox every Monday. Sign up for BizTimes’ Manufacturing Weekly at biztimes.com/subscribe.