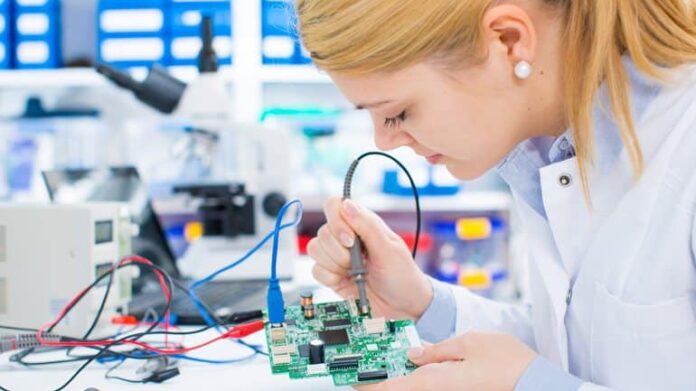
My dad worked for a large automaker for 30 years. He was proud of his job and I was proud of him. He lifted and hung car doors. In the ’70s, they didn’t use robots. Factory work was difficult and dangerous.
The first time I walked a factory floor was 1989. I toured with a group of manufacturers. It was a learning experience. There were no women on the floor. At break time, men had a restroom on the factory floor, and the women’s restroom was upstairs, in a far corner.
It was a family-owned business on the south side of Milwaukee. I was surprised by the unfriendly atmosphere. Centerfold calendars were displayed. It was a dark factory and the men seemed to have a bit of an edge. Workers weren’t engaged. There were no Lean processes or continuous improvement programs. There was a lot of wasted time and effort. As we gathered to debrief, we asked about the edgy attitude of the workers. The plant manager said it was close to union-negotiations time and workers were posturing as a show of force.
In the ’80s, workers could smoke cigarettes on the job. Some allowed beer to be served in cafeterias. Eventually, the possibility of accidents and health concerns overrode those perks.
In the ’80s and ’90s, factories began significant change. Smoking was banned. This was a shock, as many people were addicted to smoking. Companies tempered non-smoking policies with designated smoking areas, and smoking pagodas were erected just off site. Companies offered counseling and medical help to assist workers. I toured a company in downtown Milwaukee that taped off smoking areas. Workers would stand around the marked-off areas, holding their cigarettes over the smoking area in defiance of the new rule. On another tour, the VP of operations was faced with a worker boldly standing with his arms crossed and a smoking pipe hanging from his mouth.
Work-related accidents were common. Machines operated without guards. Eye protection, clothing restrictions, and safety footwear were not enforced.
Change was in the air. Some companies were stuck, but others were making strides.
Manufacturers wanted to improve for several reasons. There was waste in the way production lines made product. There were safety issues, inadequate lighting, dangerous machine functions, contentious relationships with unions, and an unfriendly environment for women. You would be hard-pressed to find a training room and even more hard-pressed to find a company who made time to develop their organization and their leaders. Factories had a long way to go, but they had a strong will to change.
Midwest factories began adopting Lean principles. Production processes were introduced. A company that introduced cellular production lines (cells) was greeted by workers wearing striped T-shirts in protest. “If we are going to work in cells, then we will look like prisoners!” Today, that company is a forerunner of continuous improvement and Lean processes.
Fast-forward 30 years. The comparison of the past and present is remarkable. Most facilities are clean and safe environments. The factory setup is different and focused on velocity and efficiency. Companies operate with teams to allow for collaborative work. Decision-making happens on the factory floor, where the work is done.
New and improved factories require a different set of managers. Organizational and leadership development are high priority.
Today’s factories will impress you with their sophistication. Computer-aided technology, robotics, and a new class of workers all contribute to the drastic change. Workers are hired based on their potential to help with growth and improvement. Today’s workforce is sought after, well trained and continually developed. Workforce diversity is written into mission statements and strategic plans.
You may be struck by the level of global knowledge that manufacturers exhibit today. Most are involved with worldwide competition. Technology enables improvements but also enables competitors in areas that didn’t exist before. American factories are located across the globe.
Today manufacturing companies are team-based and focused on the customer. Teams are engaged in customer calls, and those calls may be anywhere in the world. Manufacturing is fast-paced and ever changing. It is THE place to be for opportunity and excitement. This is not your father’s factory anymore.