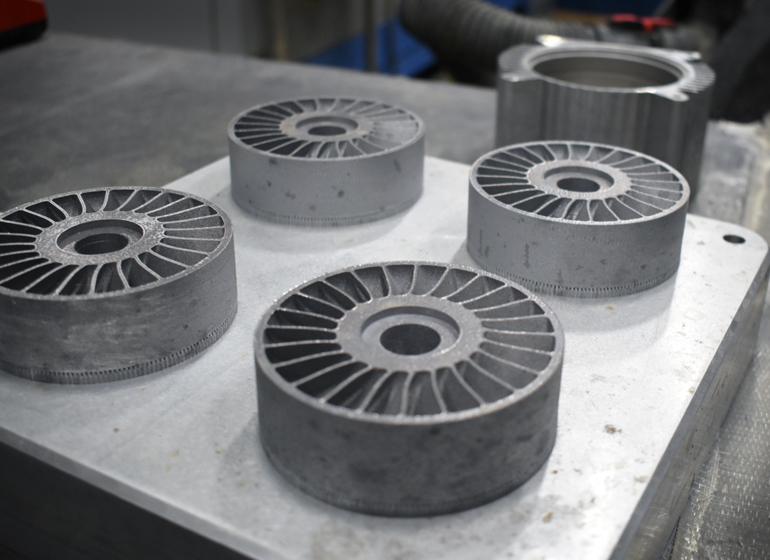
There is a good chance in a few years you will ride a motorcycle, buy a home appliance or fly in an airplane with parts in it that Midwest Composite Technologies LLC is helping design right now.
The Hartland-based company specializes in helping companies with new product development and low-volume production. It has been that way since Helmut Keidl started the company in 1984. Within the past 10 to 15 years, MCT has increasingly focused on using additive manufacturing, or 3D printing.
Core Industrial Partners, a Chicago-based private equity firm, acquired Midwest Composite Technologies last year. Ryan Martin, a former GE Additive executive, joined MCT early this year as chief executive officer.
Martin said the company has the advantage of decades of expertise developed by the Keidl family and Core Industrial Partners provides additional capital to continue to invest in growing the business. He added that additive manufacturing opens up new design and engineering possibilities.
“In traditional manufacturing, the more complex you make a part the more expensive it is,” Martin said. “In additive, complexity in a lot of these parts you can sort of get for free.”
He pointed out the most expensive thing to print with any material is a solid block. Designing complex parts with an eye toward using less material actually reduces the cost of printing each part. Since 3D printing builds things one layer at a time, parts can be designed differently.
“You have incredible freedom of design,” Martin said. “That ability to think very organically and nontraditionally allows people to come up with some pretty unique concepts … you can create things that go around components, you can do curved, you can do circular, you can have intercooling chambers just built into the parts.”
He said large manufacturers increasingly understand how to design things for additive manufacturing, although there are limitations to the technology.
“If you’re just taking a part that was traditionally manufactured and then producing it additively, there’s not a ton of value in that,” he said. “Where there is a ton of value is when you look at the part and you entirely redesign it.”
Midwest Composite Technologies works with Fortune 500 companies and their suppliers, primarily in the medical device, agriculture, transportation, aerospace and general consumer industries, Martin said. About 70% of the work focuses on creating prototypes, while the remaining 30% is low-volume production.
In many cases, MCT is working with companies on components and parts of their products, making them lighter or stronger, consolidating parts, or improving them.
“Where we’re really assisting them is rapid iterations,” Martin said, noting a company can go from a computer assisted design file to a finished prototype in hours or days because of 3D printing. “They can send us a file this afternoon, we can build that overnight or even during the day sometimes, ship it to them and they can have it on their desk.”
Speed is an advantage for MCT. Martin said the company recently had a medical device customer that was developing a new product and long lead times for a metal casting part were delaying development. Instead of waiting, MCT was able to print 25 of the parts and allow the customer to build demo models.
Midwest Composite Technologies has 45 additive manufacturing machines with capabilities in both metals and plastics. The company, however, focuses on more than additive manufacturing. Martin said MCT also does CNC machining, injection molding, fiberglass part fabrication, mold and tool making, finishing and painting.
“Typically the people that are coming to us are engineers,” Martin said. “It’s their design, it’s their product and so on our side of things, an area we’ve invested significantly in is our sales engineers.”
He said the company tries to work collaboratively with OEMs to understand what a prototype is intended for and what challenge the customer is looking to solve. Sometimes a part is for testing, other times it is for a demonstration. The challenge could be to reduce lead times or cost or potentially to change material. From there, having a variety of manufacturing methods available gives MCT options, Martin said.
“If you’re an OEM, that’s a reason why you come to us,” he said.
Midwest Composite Technologies LLC
1050 Walnut Ridge Drive, Hartland
INDUSTRY: Additive manufacturing/prototyping
EMPLOYEES: 65