Milwaukee-based Rockwell Automation and Milwaukee-based ManpowerGroup plan to have the infrastructure in place to train 1,000 veterans per year in advanced manufacturing, but the chief executives at both companies said reaching that target will require interest from potential employers and balancing the quality of training with program growth.
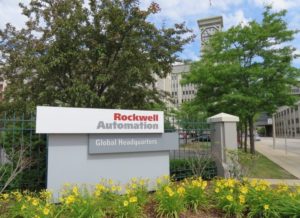
“We have a plan in the bank to build out what’s required by 2020,” said Joe Allie, Rockwell director of global competency.
Blake Moret, Rockwell chairman and chief executive officer, said the timeline is “pretty quick” considering the Academy of Advanced Manufacturing was just an idea less than a year ago. Rockwell and Manpower announced they would aim to train 1,000 veterans per year last June and ran an initial pilot class in Cleveland last fall.
Rockwell has training facilities in Ohio it has used for its own employees for a six-month training program for decades. The AAM puts veterans through a more targeted program that runs over 12 weeks. It prepares the veterans to work on a technician level on equipment on a factory floor.
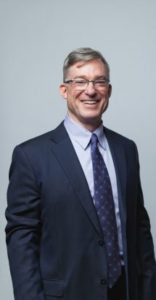
While the pilot class was underway, Rockwell invested $2 million to build out a lab and classroom space at its corporate headquarters in Milwaukee. Allie said establishing the training in Milwaukee was straightforward, but some of the logistical elements of bringing training here presented challenges. The company eventually partnered with the University of Wisconsin-Milwaukee for housing and also had to find transportation for veterans who came from around the country.
A group of 23 veterans, the first to go through the Milwaukee program, graduated from the program Thursday and 16 already have jobs lined up.
Moret said the two companies plan to graduate 150 veterans this year.
“We’re off to a great start from a program perspective,” said Jonas Prising, Manpower chairman, president and CEO.
Prising said Rockwell and Manpower had hoped to uncover skills adjacencies where certain military skillsets transferred easily to advanced manufacturing settings.
“What’s really been encouraging has been that hypothesis has been realized in a way we find really gratifying,” he said.
The companies plan to continue to expand the program, but Prising said it is important to balance growth with quality instruction.
Moret said the early success is good, but scaling the program up will require finding what he termed “anchor tenants.”
“There’s always going to be companies who ask for one or two here and there, but to get to that thousand you’re going to have to have companies that are hiring 40 or 50 of these employees a year,” Moret said.
Many of the AAM graduates end up working for Rockwell customers and Moret acknowledged it is a shift for the company to be providing employees instead of hardware or software.
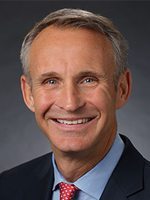
“It’s the kinds of deeper relationships that we’re seeking to build,” he said. “We’ve moved from hardware to a large amount of our offering is software and we’re adding the services that 20 years ago were more of an afterthought or a sales concession.”
He said benefits go beyond getting goodwill and closer relationships with customers because it puts people in place trained on the latest Rockwell technology.
Prising said the program is a good example of what happens when complimentary companies work together and added it also demonstrates the importance of providing training targeted towards the specific skills of certain populations.
“This is a really good illustration that the more targeted you can be … the better outcomes you will have,” he said.